About supercritical CO₂
Trial test
Since the critical point of carbon dioxide is as low as 32 ° C, it is possible to extract active or harmful components from heat-sensitive natural products. It is also suitable for drying tests of microstructures. In addition to this, dyeing and plating are also possible.
It is possible to visit for the experiment.
The following are available.
Supercritical CO₂ extraction system for trial test
Multi-use lab-system: maximum pressure 30MPa, maximum temperature 100℃, volume of pressure vessel 160ml, inner diameter of pressure vessel 32mm
The following systems are also available
- Large extraction system: Pressure vessel (6 Liter, inner diameter150mm), maximum pressure 30MPa, maximum temperature 100℃ (with pump and rubber heater)
- Very high pressure extraction system: maximum pressure 80MPa, maximum temperature 80℃, pressure vessel (volume 91 ml, diameter 32mm, length 111 mm)
- View cell (1) for visual observation: Maximum pressure 20MPa, maximum temperature 80℃
- View cell (2) for visual observation: maximum pressure 30MPa, maximum temperature 400℃(100℃ for CO₂), volume 2ml
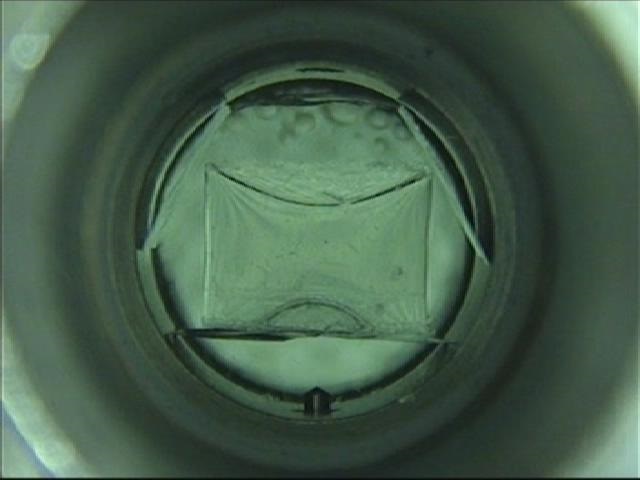
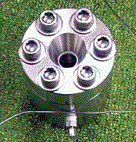
A wide variety of tests are possible within the specifications of the device. A typical example is shown below. Typical examples are shown below. (See flow examples)
- Extraction of fragrances or pigments from plants, seeds, and peels; extraction of active ingredients from hops, sesame oil, and hematococcus algae
- Degreasing, debinder, precision cleaning, purification of polymer powder (extraction and removal of volatile components)
- Aerogel, particulate solution, vegetable drying
- Particle production by controlling solubility (RESS, SAS, ASES)
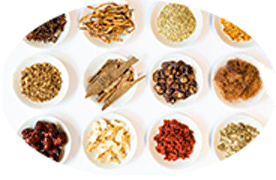
Applications
The following is a classification by object and processing.
Applicable cases of supercritical processing
Extraction / Removal
Extraction | Removal / cleaning | Drying | |
Food | Hops, sesame oil, fragrance/color Functional ingredients(*1) | Caffeine (coffe), Agrochemicals (Brown rice, carrot extract) Cholesterol (mayonnaise) | Vegetables (water) |
Wood, Polymer, Fiber | - | Cork smell (wine stopper), Monomer/dimer (resin pellet/medical material), Dirt (cleaning) Solvent (porous material) | Lacquer relics (water) |
Chemical, Cosmetic, Pharmaceutical | - | Fusel oil (fermented alcohol), Solvent/VOC (activated carbon filter), Lubricant (HDD) | Alcohol (water) |
Inorganic, Metal, Semiconductor/MEMS | Precious metals (autocatalysts), Radioactive waste | Binder/organic matter (ceramic/catalyst), Oil (metal surface), Etching residue (wafer) | Sol/gel for Aerogel/Polymer gel, Nanoparticle dispersant, Cleaning solution (MEMS/wafer) |
Impregnation / addition / adhesion
Impregnation | Staining | Plating / deposition | |
Food | Vitamins, essential oils (food powder) | - | - |
Wood, Polymer, Fiber | Antiseptic/ant agent (wood),Silica, silver, etc. (surgical tools, lenses, composite materials), Antiseptic/ant agent (wood), Silica, silver, etc. (surgical tools, lenses, composite materials), Functional ingredients (light stabilizer, water/oil repellent, conductive substance) | Tanning agent (leather), Dyes/Pigments (films/sheets, polyester fibers, cotton, optical fibers) | Plating catalysts, Films/sheets/molded products, Communications/electric wires |
Chemical, Cosmetic, Pharmaceutical | Sustained drug release antioxidant (implant material) | - | - |
Inorganic, Metal, Semiconductor/MEMS | Hole transport material (solar cell) | Photosensitizing dye (solar cell) | Electroplating, Metal/insulating thin film (wafer) |
Others
Fine particles | Foaming / sterilization / others | |
Food | Powdered fat | Pasteurization (orange juice) |
Wood, Polymer, Fiber | Polymer powder, nanoparticle dispersion composite, conductive particles | Injection molding, foaming (light reflecting sheet, auto parts, polymer alloy, graft polymerization, electrospinning) |
Chemical, Cosmetic, Pharmaceutical | Polymer-inorganic powder complex (liposome, cosmetic powder, antistatic toner, DDS pharmaceutical powder) | Hydrogenation reaction (cyclohexanone), polymerization, painting |
Inorganic, Metal, Semiconductor/MEMS | Pulsed laser, Silicon nanocrystals, Gold nanospheres | - |
——— *1 ———
Examples of food-based extracts and functional ingredients
Propolis, DHA / EPA, catechin, chamomile, α-linolenic acid, sesamin, xanthohumol, piperine (black pepper), linalool (coriander), saw palmetto / saw palmetto, fish oil fatty acid, eastern purple coneflower, evening primrose, phytosterol, tocopherol, phospholipids, etc.
Extraction example of antioxidant
Carotenoids: β-carotene, astaxanthin (microalgae), pheophytin, curcumin (turmeric), lycopene (tomato), lutein, etc.
Examples of triterpene extraction
Squalene, faradiol / alinidiol
Bold blue letters are commercialized. Items in parentheses indicate the object to be processed. This is the estimated status as of January 2020.
Carbon dioxide is present in the air at over 400ppm. Familiarly, it is also dissolved in beer. It is a gas at room temperature, but by pressurizing it, it can be liquefied even near room temperature and used as a solvent. Carbon dioxide is widely used as an extraction solvent for functional components. Recently, there have been examples of using supercritical carbon dioxide for anhydrous dyeing of polo shirts. The features and merits of supercritical carbon dioxide treatment are as follows.
Solvent
Easy solvent removal after treatment
Room temperature treatment
- Processing of food and heat sensitive materials
Physical properties can be controlled
- Variable density (generation of fine particles)
- Variable dielectric constant
- Variable solubility
- Low surface tension (no gas-liquid boundary)
Both gaseous and liquid characteristics
- Low molecular weight, low viscosity
- Low surface tension (surface tension free drying)
- High diffusion/high permeability (CVD)
- High heat flux (supercritical plasma)
Others
- Density fluctuation and clustering
- Multipole moment (chemical interaction of polymer chains, plasticizing effect)
A typical example is shown in Q4 above. Supercritical carbon dioxide is used in the extraction of functional ingredients such as health foods, flavors and dyes, hops used in beer, and sesame oil. Traditionally, extraction at 30 MPa or lower has been the mainstream, but recently even higher pressure extraction has been used (see below).
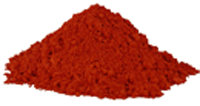
Features of Supercritical Carbon Dioxide Extraction
- No solvent residue
- Extraction can be performed at near room temperature, and the unique aroma of the raw material is preserved.
- Minimal contamination
- Low viscosity and high fluidity
(Comparison with solvent extraction of carotenoids)
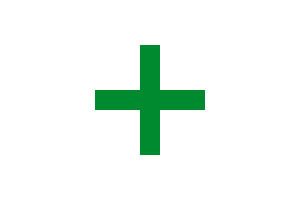
Features of high-pressure supercritical carbon dioxide extraction
- Increased productivity and reduced processing costs
- Safe and efficient extraction of small amounts of high value-added functional ingredients
- Reduction or elimination of co-solvent
At the research level, there are published examples of recovering platinum and rhodium from waste automotive catalysts by extracting them by forming complexes with chelating agents and precious metals.
A typical example shown in Q.4 is decaffeination from coffee beans. This technology started in 1978 in Bremen, Germany, and now decaffeinated coffee is produced in many countries. There is also the removal of pesticides from brown rice and carrot extract, and cholesterol from mayonnaise. In addition, in order to prevent cork odor (which occurs in 2-5% of wines) caused by microbial metabolism of a substance used as a wood preservative, called bouchonne, ultra-large equipment to remove more than 150 volatile molecules, including TCA (2,4,6-Trichloroanisole) at several ppb levels from wine corkscrews is in operation in Spain (three 11 cubic meter extraction tanks) and France (three 19 cubic meter tanks).
In the plastic film industry, porous membranes are produced by kneading supercritical carbon dioxide soluble fats into the film and removing them.
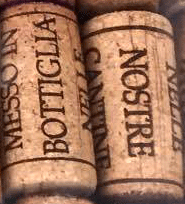
Typical examples are shown in Q.4. In the U.S. and other countries, it is used for dry cleaning of clothing and ballpoint pen balls. In Japan, contact lens cleaning, removal of VOCs and other substances from HEPA filters used in semiconductor factories, and removal of etching residue from semiconductor wafers (R&D only) have also been performed.
Cleaning technology utilizing the dissolving power of supercritical carbon dioxide is attracting attention in a wide range of fields as an environmentally friendly technology. In addition, supercritical carbon dioxide has low surface tension, which allows it to penetrate into minute spaces and clean fine patterns (semiconductor parts, precision parts, etc.) without destroying them. Furthermore, this unique process eliminates the need for a drying process. An example of a supercritical cleaning system is shown here.
Some examples are shown in Q.4. The most typical example is surface tension-free drying.
When treating microstructures, porous materials, etc. with solutions, a drying process is essential for the treated object in a wet state. In such cases, microstructures immersed in the solvent are subjected to the following phenomena.
- If flexible, the structure shrinks without compensating for the decrease in solvent as evaporation progresses
- Subsequently, as drying progresses and the surface of the structure is exposed, an interface between the gas and liquid phases appears inside the structure, and surface tension causes the structure to contract stress toward the tangential direction of the interface
These not only significantly affect the density, microstructure, shape, and physical properties of the material, but also make it more susceptible to cracking/cracking.
In supercritical drying, the liquid phase can be transferred to the gas phase via the supercritical state. During this time, the interface between the liquid and the gas never appears, and the surface tension that causes the destruction of the microstructure does not occur. This results in drying without shrinkage or damage to the object. Application examples include drying of fine resist patterns of semiconductors, drying after removing the sacrificial layer of MEMS (Micro Electro-Mechanical System), and drying of silica airgel (sold as a high insulation sheet). However, even with supercritical drying, in the presence of other solvents, an interface may be formed and surface tension may occur.
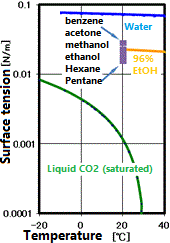
Examples are shown in Q.4. The most typical example is dyeing.In February 2012, NIKE, Inc., a global sports footwear company, announced that it wanted to promote the use of supercritical CO2 anhydrous dyeing technology throughout the industry “to benefit both athletes and the global environment”. Then, in August 2012, ADIDAS AG of Germany announced a technology called DryDye and declared its commitment to environmental contribution. It announced, “Worldwide, water equivalent to seawater in the Mediterranean Sea was consumed for dyeing in two years, but with Drydye, 1,250 tons of water was saved by dyeing 50,000 T-shirts this summer. In Japan, research on supercritical dyeing technology has been conducted since the late 1990s, led by the University of Fukui.
When supercritical carbon dioxide dissolves in an organic polymer material, it causes swelling and plasticization (i.e., relaxes the entanglement of polymer chains, promotes their mobility, and increases their free volume). For example, polycarbonate (PC) is generally considered an amorphous polymer, but up-hill diffusion by spinodal decomposition of PC and carbon dioxide is thought to induce PC crystallization. These features can be used to dye polyester fibers and other materials that were previously considered difficult to dye with zero wastewater.
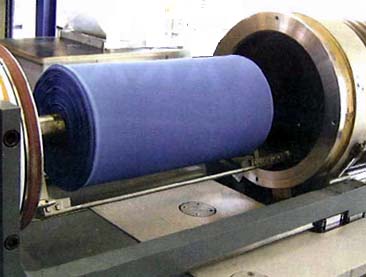
Effects of carbon dioxide on polymers
- Decrease in Tg
- Decrease in viscosity
- Decrease in surface tension
- Increase in diffusion coefficient
- Facilitation of crystallization
Apparatus
For supercritical processing, the following items are required at a minimum: a pressure vessel for the material to be processed (“extractor” shown on the right in Q.12), a pump that pressurizes to about 5 to 45 MPa, a heater that keeps the temperature at 20 to 150°C, a separator to separate the extracted material from the CO₂, and a CO₂ cylinder.
To manufacture the equipment, specifications such as the capacity of the pressure vessel, design temperature, design pressure, and flow rate are first determined according to the treatment purpose and treatment volume. For example, if you want to observe the supercritical condition (~ 27MPa), use the view cell with a glass window shown in the Q.2. The system can be fabricated from 5 ml or more. In the case of a test system, cooling and recovery of carbon dioxide as shown in Q.12 is not generally done for economic reasons.
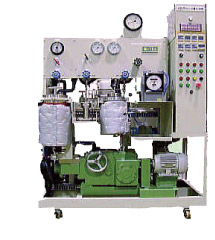
Please refer to Q.2 for the apparatus used in our trial test. The following are examples of typical equipment manufactured by our company.
Pilot plant
50MPa、80℃、30 Liter
The production system will be larger than the bench plant and pilot plant (see Q.11). In this case, since the amount of carbon dioxide released into the atmosphere is large, it is usually cooled and liquefied and recycled (see the figure on the right). In addition to the figure on the right, there are cases where an entrainer pump is added.
Please refer to other sections for the size of the processing container (Q.13), CO2 supply and recovery (Q.15), law application and greenhouse gases (Q.16).。
The following is an example of our delivery.
- Supercritical CO₂ extraction plant: extractor 250 Liter x 2, maximum pressure 50MPa
- Supercritical CO₂ extraction plant: extractor 380 Liter x 1, maximum pressure 38MPa
- Supercritical CO₂ extraction plant: extractor 500 Liter x 3, maximum pressure 30MPa
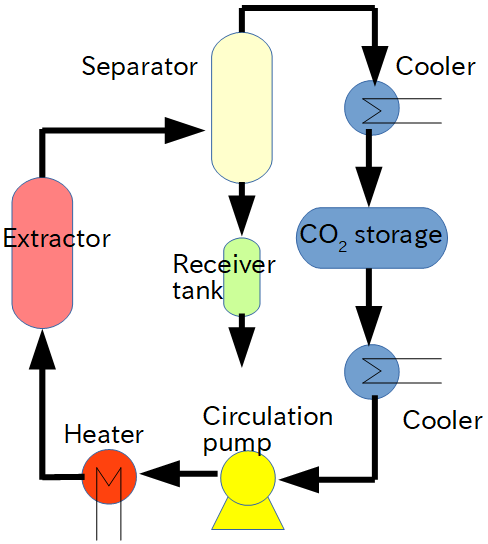
In domestic extraction plants, it is common to use several 100-500 liter extractors. Examples from around the world have produced large pressure vessels (up to 6500 liters), as shown on the right figure. The plant for processing wine cork stoppers (Q.7) that went into operation in France has three 19,000-liter extractors with a pressure of 13 MPa (2015). However, there are various restrictions to install such a large scale pressure vessel, such as transportation, applicable laws and regulations in the country of installation (especially the High Pressure Gas Safety Act in Japan is very strict), and so on.
The pressure vessel capacity and flow rate determine the time required for pressurize. It has extremely high variability, as shown in the figure on the right.
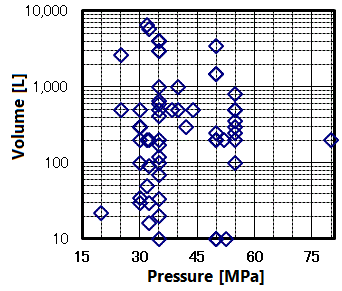
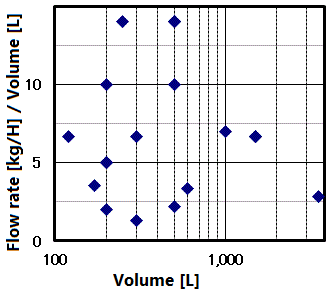
The pressure for supercritical processing is often 10 MPa or higher. Since it is difficult to continuously feed solids into a high-pressure vessel, batch processing is used. To facilitate batch processing, the pressure vessel is equipped with a rapid lid opening/closing mechanism as shown in the picture. This makes it easy to load and unload materials to be processed. Normally, multiple pressure vessels are installed. The reason is that the alternative use of these pressure vessels enables continuous operation of carbon dioxide supply and recovery, which is economical.
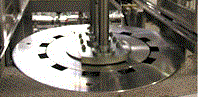
In large systems, carbon dioxide is recycled. As shown in the flow chart of A.12, carbon dioxide flowing from the extractor is generally reduced to 4 to 6 MPa or less (below the critical point). At this time, the temperature drops and it becomes two phases, a gas phase and a liquid phase. Then heat it to a gas and the dissolved substance will separate. The remaining carbon dioxide gas is stored in the storage tank after being liquefied by the cooler. This liquefied carbon dioxide is cooled further (about 5-10 ° C below the boiling point) to prevent it from vaporizing. It is then pressurized by a circulation pump and fed back to the extractor.
This figure shows the heat of condensation and the load and power of the cooler as a function of pressure. The lower the pressure, the more energy is needed to turn the gas into a liquid. Also, the lower the temperature, the lower the operating efficiency of the cooler. For example, the heat of vaporization at 6MPa and 2MPa is doubled, while the power consumption is about 5 times. That is, efficiency is significantly reduced at low pressures. In the actual design, the terms of use with the separator are also taken into consideration.
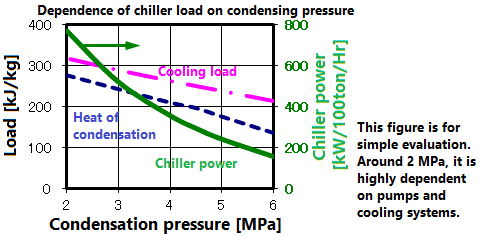
Legal regulations
The user is required to notify or permit the use of high-pressure gas to the prefectural office.
The “high pressure gas” specified in the High Pressure Gas Safety Act corresponds to a) compressed gas of 1 MPa or more, b) liquefied gas of 0.2 MPa or more. Liquefied carbon dioxide is also applicable (vapor pressure at 20 ° C is 5.6 MPa).
Notification to the prefectural office is required for Type 2 manufacturers. If only CO2 gas for supercritical equipment is used in the office and the processing amount is 300 Nm³ or less in 24-hour conversion, it corresponds to the Type 2 manufacturers. The details vary from case to case, but are roughly as follows.
When exhausting used CO₂ without reusing it
12kg-CO₂/Hr / 44 kg/kmol x 22.4 Nm³/kmol x 24 Hr x 2(pressurization and heating) = 293 Nm³/day < 300 Nm³/day
When recovering used CO₂ and recycling it
8.1kg-CO₂/Hr / 44 kg/kmol x 22.4 Nm³/kmol x 24 Hr x 3(pressurization, heating and condensation) = 297 Nm³/day < 300 Nm³/day
If you use it at a flow rate higher than the above, apply for permission from the prefectural office because it corresponds to a type 1 manufacturer. You must pass the completion inspection after getting permission. The user needs to prepare the application documents, but the manufacturer usually prepares the documents related to the device.
Type 1 manufacturer (licensed by the prefectural governor; see Q.16) must appoint a safety officer (a person who has been issued an exemption from production safety responsibility and who has experience in the production of high pressure gas).
According to the internal regulations of the Ministry of Economy, Trade and Industry, it is possible to appoint a safety officer who belongs to another company if some conditions are met if there is no experienced person. For that purpose, it is limited to the case where the duties and authority related to the safety office are clearly defined in the regulations and the consignment contract, and it can be confirmed that the duties can be performed reliably.
If the carbon dioxide processing capacity of the device is 30 m³ / day or more, a self-inspection is required every year. In addition, if you are a type 1 manufacturer, you need to carry out a safety inspection by the prefectural office.
The safety inspection will be taken one month before and after one year has passed since the day of the previous safety inspection (in the case of the first time, the day of the completion inspection).
Self-inspection includes pressure gauges, thermometers, and safety valve inspections, wall thickness measurements, and airtightness tests. When handling non-corrosive gas, open inspection is performed every 3 years. In the safety inspection, the prefectural office checks the self-inspection report, safety officer’s license, etc., and also witnesses the airtightness test. Since the contents differ depending on the prefecture, it is necessary to confirm the inspection contents in advance before the safety inspection.
Carbon dioxide used in supercritical processes is emitted as a reaction by-product from ammonia production and petroleum refining plants. This is collected and liquefied for reuse. However, because it is the final stage of emissions, it is probably considered a greenhouse gas emitter.
According to the method of calculating greenhouse gas emissions described in the materials of the Ministry of the Environment, for example, a person who collects carbon dioxide during the ammonia production process and provides carbon dioxide to others is not considered to be an emitter. On the other hand, when the carbon dioxide is reused (for example, dry ice production), it seems to be an emitter. Therefore, even when used in a supercritical process, it can be a emitter.
General
Please contact us.
“Supercritical fluid NET” operates the following website (Japanese).
In processes using supercritical fluids, especially in carbon dioxide separation or regeneration processes, high-pressure fluids are decompressed. To determine the phase and temperature of carbon dioxide during this time, the Mollier diagram (below) is used. From the initial state to the final pressure, draw a vertical line downwards to check. This diagram allows us to determine not only the temperature but also the ratio of gaseous carbon dioxide to liquid or dry ice. This diagram utilizes the fact that enthalpy does not change during free expansion.
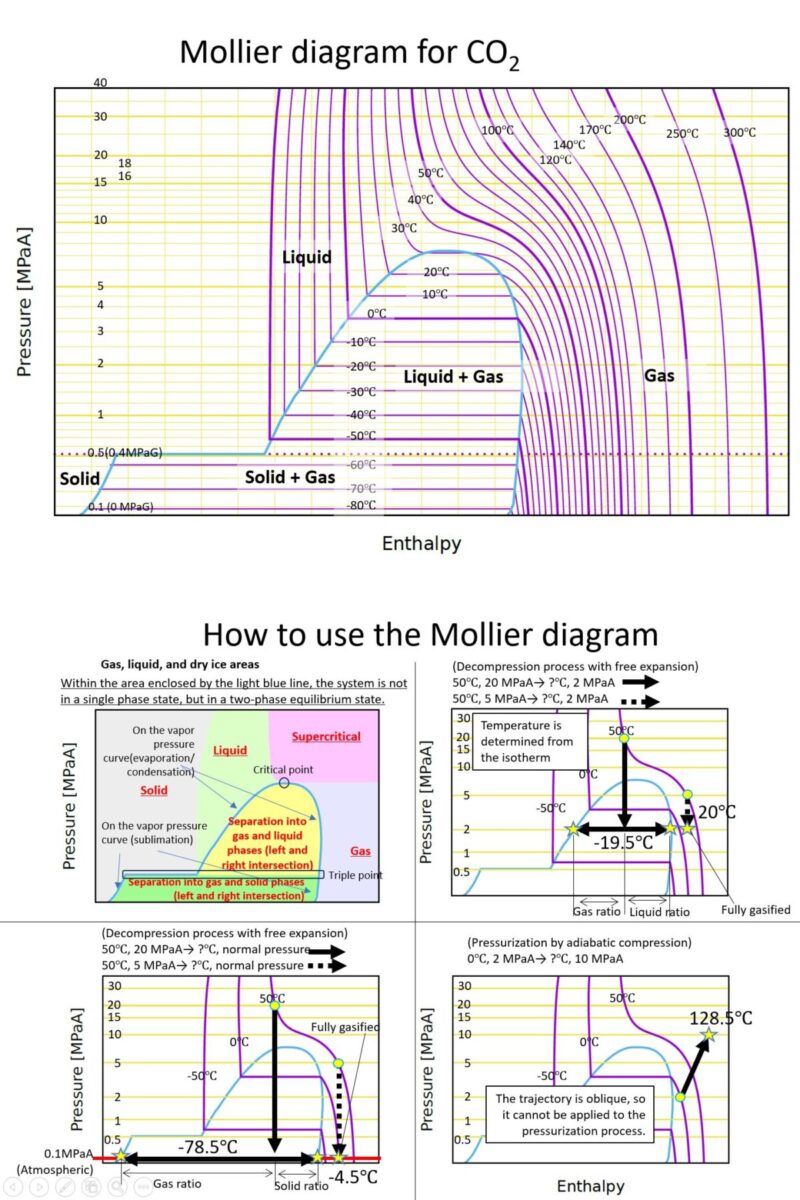